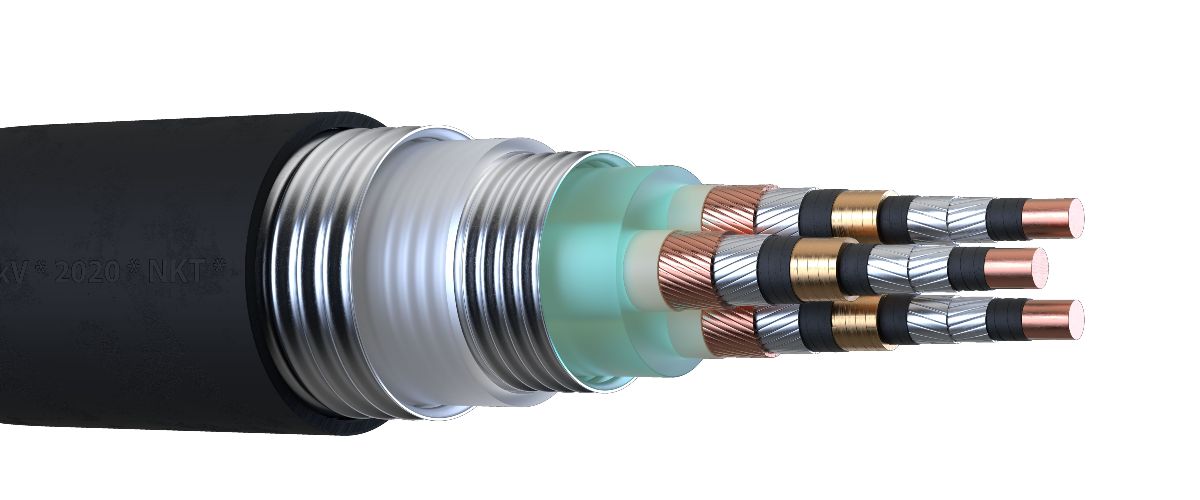
Hochtemperatursupraleiter für die Energiewende
Über eine Distanz von einem Kilometer verbindet ein Supraleiter-Kabel in Essen unter der Erde zwei Umspannwerke und versorgt mehrere tausend Haushalte mit Strom. Im Vergleich zu Kabeln aus Kupfer oder Aluminium transportieren HTSL-Kabel Strom ohne Verluste und sind platzsparend. Das macht die Technologie für die Stromwende besonders wichtig.
Während in Leitern aus Kupfer oder Aluminium ein Teil des Stroms in Verlustwärme umgewandelt wird, leitet das Supraleiterkabel elektrischen Strom nahezu widerstandsfrei und trägt bei gleichem Durchmesser circa fünfmal so viel Strom. Eine innovative Lösung, um Städte mit zunehmendem Strombedarf in Zukunft mit Strom zu versorgen, und ein wichtiger Beitrag für die Energiewende. Wie das funktionieren kann, zeigt etwa das Forschungsprojekt AmpaCity in Essen, das mit dem Deutschen Innovationspreis für Klima und Umwelt (IKU) ausgezeichnet worden ist.
HTSL-Kabel: Kühlen mit flüssigem Stickstoff
Hochtemperatursupraleiter (HTSL) nutzen die Eigenschaften spezieller keramischer Materialien, deren elektrischer Widerstand unterhalb einer bestimmten Temperatur nahezu verschwindet. Flüssiger Stickstoff kühlt die flachen, dicht aneinander liegenden Leiterbänder, durch die der elektrische Strom transportiert wird, auf minus 196 Grad Celsius.
Um Kühlverluste gegenüber dem Erdreich zu vermeiden, müssen HTSL-Stromkabel wie eine Kanne sehr gut wärmeisoliert sein. Die Forschung entwickelt derzeit energieeffiziente sowie kostengünstige, zuverlässige und wartungsarme Kälteanlagen.
HTSL machen Industrieanlagen, Maschinen und Motoren energieeffizienter
Die HTSL-Technologie lässt sich auch in Industrieanwendungen einsetzen, etwa in Motoren, Generatoren, Induktionsheizern oder Stromschienen.
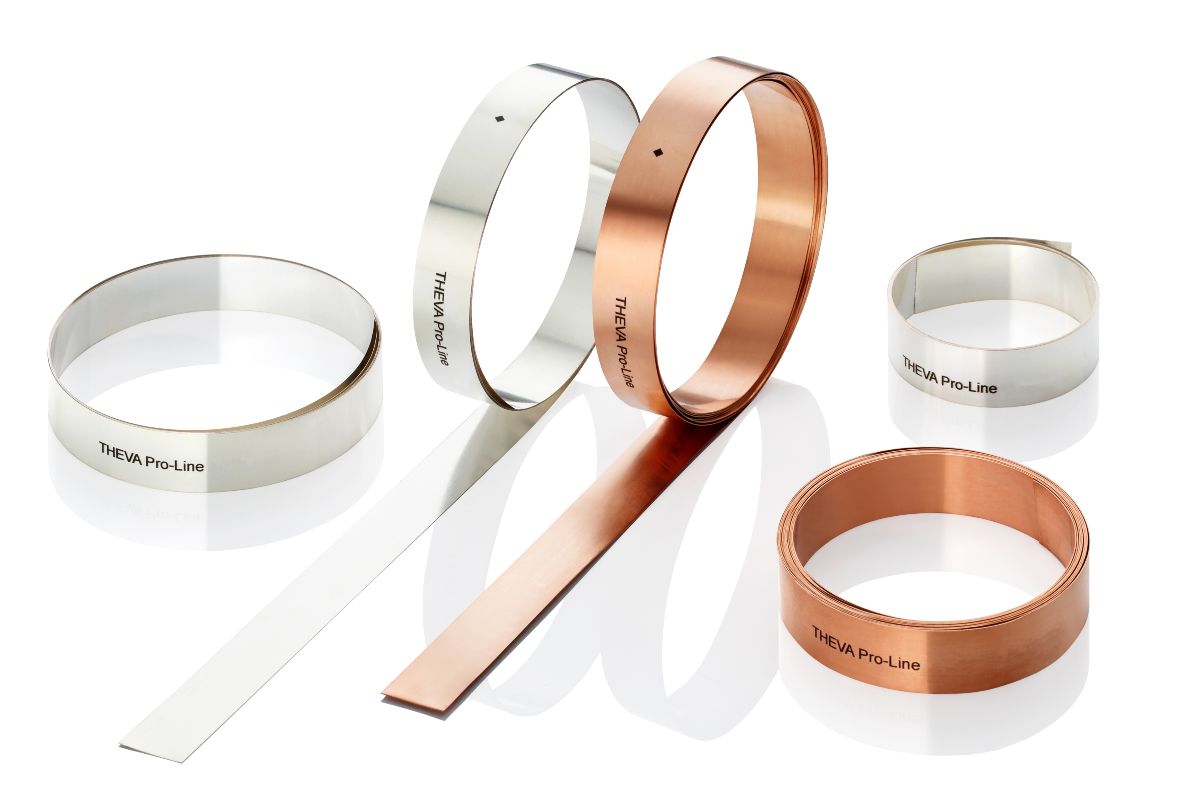
Stromstärken von mehreren hundert Kiloampere kommen in Elektrolyseanlagen der Grundstoffindustrie zum Einsatz – etwa für die Herstellung von Chlor, Kupfer oder Aluminium. Wenn diese Ströme künftig durch kompakte supraleitende Hochstromschienen geleitet werden, entfallen die erheblichen Energieverluste durch den elektrischen Widerstand.
Rotierende Maschinen, wie Motoren und Generatoren, können gegenüber konventioneller Technologie bei gleichen Abmessungen leistungsstärker und energieeffizienter ausgelegt werden – oder bei gleichen Leistungsdaten kompakter gebaut werden. Selbst im oberen Bereich des Leitungsspektrums elektrischer Generatoren mit sehr gutem Wirkungsgrad ermöglicht die HTSL-Technologie, diesen um die letzten Zehntelprozentpunkte zu steigern.
Forschung will Produktionsvolumen, Kosteneffizienz und Leiterqualität verbessern
Betriebserfahrungen mit Supraleitern in Maschinen und im Netz liegen inzwischen vor und haben in kleinen Maßstäben gezeigt: die technischen Anforderungen können erfüllt werden. HTSL ermöglichen einen erhöhten Wirkungsgrad, ein kompaktes Bauvolumen und eine hohe Leistungsdynamik. Die Zuverlässigkeit ist nachgewiesen, und auch die Kosten nähern sich dem Niveau von konventionellen Systemen.
Mittelständische Unternehmen im rheinischen Rheinbach und im bayerischen Ismaning stellen in jeweils unterschiedlichen Verfahren – Vakuumbedampfung beziehungsweise chemische Beschichtung – HTS-Leiter im Maßstab einer Pilotfertigung her. Je nach Marktdurchdringung der HTSL-Komponenten wird sich ein zukünftiger Bedarf von Zehntausenden Kilometern HTSL-Draht pro Jahr ergeben. Im Vergleich zur ersten Generation der HTSL-Drähte, die zu 60 Prozent aus Silber bestehen, kommen die neuen HTSL-Bandleiter der zweiten Generation nahezu ohne teure Rohstoffe aus.
Forschende haben erfolgreich daran gearbeitet, die im Labor gefundenen Leitereigenschaften zu verbessern. Aus den spröden, keramischen Materialien lassen sich mit industriellen Verfahren supraleitende Drähte oder Bänder in der erforderlichen Qualität herstellen. Für wirtschaftliche Anwendungen werden nun skalierbare Fertigungsmethoden entwickelt, um die benötigten HTSL-Mengen bei durchgehend hoher Qualität sowie konstant hoher Stromtragfähigkeit kostengünstig herzustellen. Ein hoher Automatisierungsgrad wird dazu beitragen, den zunehmenden Bedarf an HTSL-Material „made in Germany“ zu decken.