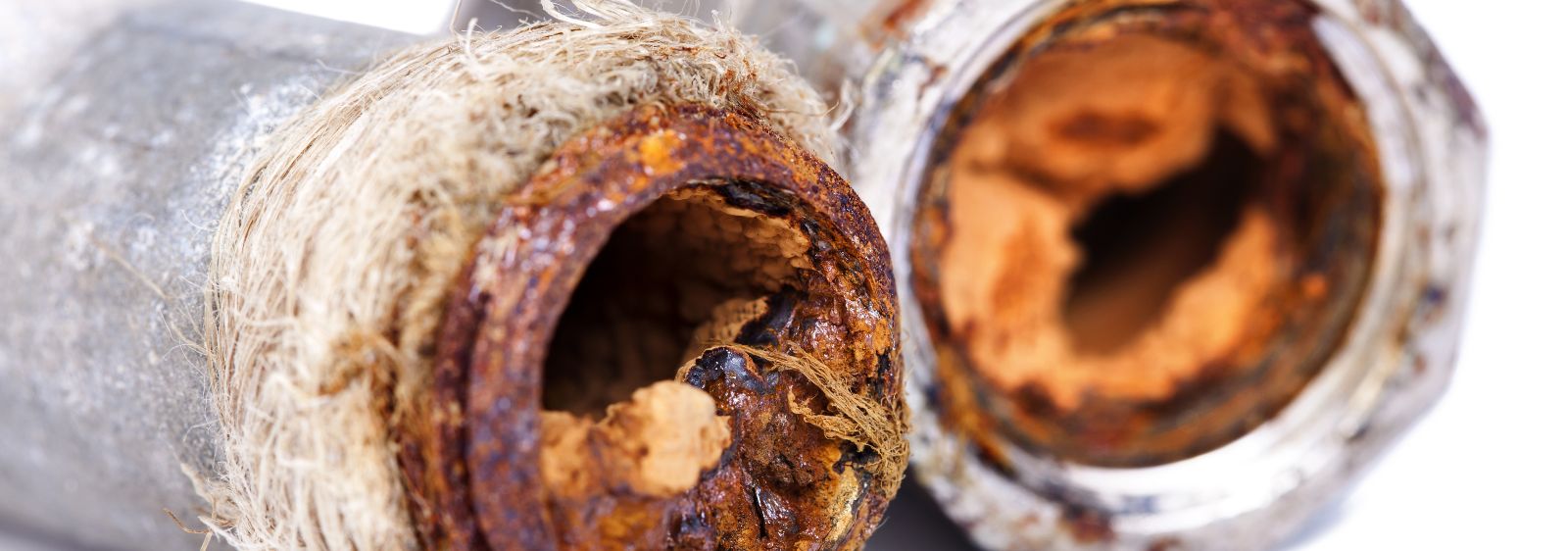
Ventilation systems
Corrosion in hydraulic systems
With this research project, corrosion processes are being investigated in heating and cooling systems. In addition to laboratory tests, a field test is also being conducted where real buildings will be evaluated in energy terms. At the same time, corrosion and anti-corrosion measures are being evaluated with a newly developed corrosion sensor. Based on the experience gained in the project, work is being conducted on guidelines to help designers prevent corrosion and to document possible remedies.
Modern heating and cooling systems have significantly different properties in comparison to older systems. However, the relevant technical regulations and standards have not kept pace with the rapid development during the past 20 years. Lower system temperatures and increasingly more plastic components improve the living conditions for micro-organisms and diffusing oxygen causes lasting corrosion processes. At the same time, precision mechanical valves, high-efficiency pumps and capillary tube mats tolerate significantly fewer particles in system fill-up water and make the systems more vulnerable to deposits and corrosion products.
In the project it is intended to develop suitable planning guidelines, check lists and tools for quality management in practice. Among other things, a sensor system is being tested that measures both the system state as a whole as well as many relevant individual parameters and also makes it possible to evaluate specific systems.
Research focus
Corrosion in heating and cooling systems is caused by a variety of reasons and the individual processes are not widely known. However, in-depth knowledge of the processes is needed for monitoring, diagnosis and remedial action. Moreover, quality management tools are increasingly required in practice to monitor, structure and document operational processes. In addition, remedial measures need to be tested and examined in terms of their practicability in order to generate substantial application knowledge and guarantees.
Successes
Previous studies have clearly demonstrated the complexity of the various systems, water processing and treatment strategies and processes involved. It has also been found that cooling systems are particularly vulnerable if they are filled with untreated water – or are filled with incorrectly treated water – due to the lack of technical regulations for this area. Seemingly in accordance with VDI 2035, they are often filled with softened water, which depending on the raw water quality generally provides, however, insufficient protection against corrosion. In conjunction with diffusing oxygen or microbial processes, this results in corrosion damage.
It has been shown, however, that corrosion occurs much less frequently with heating systems because higher temperatures prevail here, treated water is used more often and surface heating and cooling systems are used more rarely. From the water chemistry point of view, the fault that occurs most often here is that the degree of hardness is too great in relation to the VDI 2035 requirements.
The project results will be incorporated in the findings of the BTGA Committee on Corrosion in Closed Cooling and Cold Water Systems (Sheet 3002-2).
Application
Field tests are currently still being carried out in different buildings. The eight most interesting buildings will be subsequently included in more intensive investigations that also include energy monitoring and continuous corrosion measurements. Remedial measures will then be conducted and tested in three of these buildings.