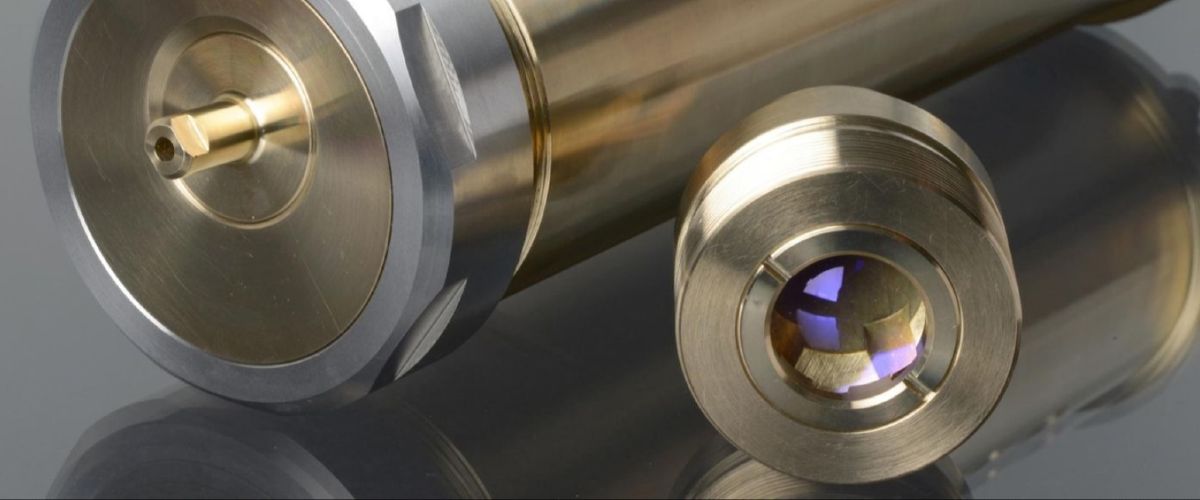
Geothermal energy
Laser beam accelerates geothermal drilling
Three to five kilometres sometimes have to be drilled in order to make extensive use of geothermal energy. During this process the drills encounter different materials, including very hard rock. These delay the drilling progress and wear out the drilling tools. Scientists have developed a new process within the LaserJetDrilling research alliance: they have added a laser to the mechanical drill. The laser beam is guided within a water jet onto the rock and makes it porous. The water jet directs the laser beam and protects the sensitive laser optics with its mirrors and lenses. Initial field tests have already been successfully completed.
Drilling components wear out faster
The aim of all geothermal drilling is to achieve a high penetration rate, i.e. drill deep underground quickly. Purely mechanical drilling is currently used, for example with rotary bits. In order to accelerate the drilling process, researchers are investigating hydraulic methods or electro-pulse drilling, which uses high-energy electrical discharges. The aim in each case is to weaken or destroy the rock.
If the drilling is carried out through very hard rock such as granite and quartzite, the individual components of the drilling rig wear out very quickly. This is where the LaserJetDrilling research project comes in, whose full project title is “Development of a water jet-guided laser drilling technology for the efficient exploitation of geothermal resources”. The central approach is to couple a high-power laser water jet with a mechanical drilling process for the first time.
Laser beam causes the rock to fracture
Usually the rock is broken up mechanically. Sensors in the drill head measure the torque and driving force of the drill. This enables the drilling process to be adapted to the hardness of the material. With very hard stone such as granite and quartzite, the mechanical drilling systems reach the limits of their resilience.
In the LaserJetDrilling process, a high-energy laser beam first damages the rock. The cohesion between the crystals in the stone is loosened and fractures appear. This allows the mechanical drilling tool to be driven through the rock more quickly. The laser beam is intended to be used in accordance with the hardness of the rock. The new procedure speeds up the work and facilitates deep drilling for new geothermal plants.
New laser head supplements the drill head
The project partners have supplemented the mechanical drill with a high-power laser. Its energy is directed onto the rock using a water jet. To focus the laser beam, they have developed a laser head, beam source and fibre-fibre rotary coupler. The challenge here is to transmit the laser beam from the non-rotating laser source via an optical fibre made of quartz glass to the fibre in the rotating drill string. This is achieved using the newly developed fibre-fibre rotary coupler, which decouples the fibres and transmits the laser beam from the non-rotating to the rotating fibre. This safely guides the beam to the drill head.
Further studies were also partly concerned with the interactions of high-power laser beams with a laminar water jet. Water absorbs the beams and heats up. If the water jet becomes too hot, it can evaporate. To prevent this from happening, the researchers determined the necessary amount of water in the jet. They then developed initial prototypes for a laser head and the associated drill head, and integrated these components into a drill string.
First test rig with a high-power laser
The scientists tested the high-power laser beam on a laser test rig that was specially designed and created for this purpose. This is located at Fraunhofer IPT, which provides the necessary infrastructure for the laser source as well as the cooling power and electrics. The laser test rig enables experiments with 30,000 watts of optical power. The test results have shown that the laser-irradiated rock samples lose about 40 to 60 per cent of their strength.
Following successful tests on the test rig, the project partners have integrated the laser technology into a drill string. The complete system consists of the laser source, laser, cooling unit and pump for the water as well as the drilling equipment. They have set this up on the drilling site at the International Geothermal Centre (GZB) in Bochum. The laser and drilling technology successfully passed the subsequent tests.
In future sensors will control the energy of the laser beams
In a follow-up project, the scientists plan to better distribute and dose the laser’s power. To achieve this, the drill head will be supplemented with digital sensors. The data obtained comes directly from the borehole. This will allow the mechanical drilling process and the laser’s energy to be adapted directly to the existing rock along the drilling path.