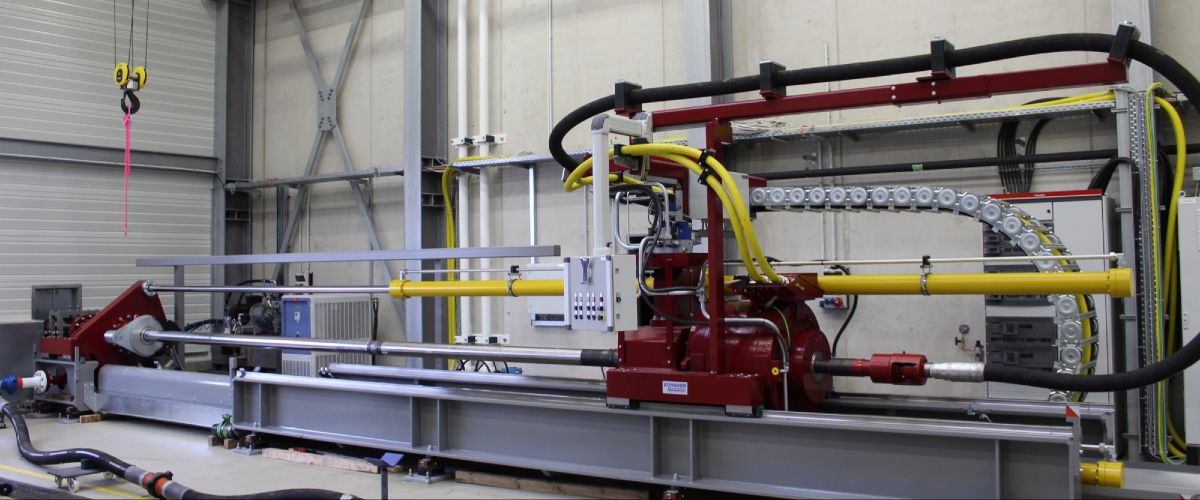
Geothermal Energy
Detecting and preventing vibrations in drilling systems
The research project is focusing on the targeted, safe and cost-efficient drilling of wells up to several thousand metres deep. Undesirable vibrations of the drilling equipment need to be better controlled in order to reduce the high drilling costs. In the research project, teams of scientists are systematically investigating the vibration behaviour of drill string components using a laboratory method in order to determine the type of vibration and its causes. The results should help prevent vibrations during the drilling process.
Project context
A particular challenge in geothermal energy is to safely reach the target range when drilling up to several thousand metres. This can cause vibrations in the drill string, especially when the drill is drilling through irregular fault zones in the rock. This can damage the drilling systems or even cause them to fail. The drilling progress is hampered because the bit temporarily loses contact with the rock. Overall, this shortens the service life of the bit, the drilling makes less progress and high costs are incurred.
The research project aims to optimise the progress when drilling deep geothermal wells by systematically investigating and analysing the vibration behaviour of drill string components.
Research focus
The aim of the project is to make geothermal drilling more economical by investigating drill string vibrations under laboratory conditions. In the next step, these investigations will be processed to provide recommendations for action for industry. The special feature here is the use of a globally unique, horizontal full-scale drilling test rig. This enables drill string vibrations in the lower 20 metres of drill strings to be investigated holistically under realistic conditions. The vibrations are caused by real drilling processes. The behaviour of real drill strings (for example with 4000-metre lengths and more) can be simulated by extending the existing drill test rig with actuators and virtual drill string models.
Innovation
The globally unique drilling test rig makes it possible to drill under realistic conditions and to investigate this process. Other test rigs ignore essential physical and geometrical aspects (for example, flow loop test rigs, test rigs for BHA dynamics, etc.). The hardware test rig at the Drilling Simulator Celle (DSC) simulates the entire horizontal drilling process. Vibrations caused by the missing drill pipe are simulated by models and actuators. This requires a real time-capable control system, which among other things must also evaluate and process drill string data in real time. An autoclave makes it possible to drill into rock samples under the influence of mud, pressure and with a realistic tool load.
Results
A rock sample chamber was developed in which rock samples can be drilled under appropriate pressure. The first drill test in sandstone with a Polycrystalline Diamond Compact (PDC) chisel took place in February 2018. Initial real-time drill string models have now been developed.