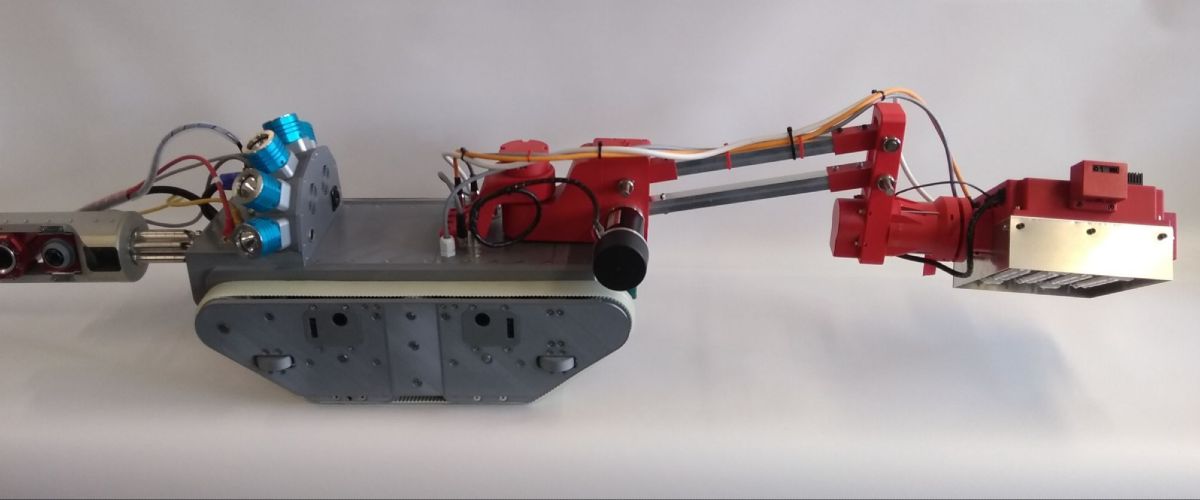
Wind energy
Robot checks rotor blades from the inside for production defects
Damage on the inside of rotor blades can now be detected more easily and comprehensively. A new thermography robot makes this possible.
Within the "ThoR" project funded by the German Federal Ministry for Economic Affairs and Energy (BMWi), researchers have developed a thermography robot that can detect production defects near the surface inside rotor blades. This increases the safety and economic efficiency of wind turbines, because material defects such as faulty bonding and cracks can have serious consequences, including failure of the entire plant. Therefore the rotor blades must be carefully inspected from the inside and outside. "Inspection from the inside was previously only possible to a limited extent because not all areas of the blade are accessible and not all defects are visible," says Jochen Aderhold, project manager at the Fraunhofer Institute for Wood Research, Wilhelm-Klauditz-Institut WKI.
Thermography robot detects damaged areas
Rotor blades of wind turbines are complex components. The rotor diameters are constantly increasing and the geometry of the blades is becoming increasingly complicated. This is intended to improve aerodynamics and reduce noise emissions. The manufacturers use various materials, including glass and carbon fibre reinforced plastics with polyester or epoxy resins as the basis, as well as balsa wood, foamed plastics and metal. This mix of materials with elements of poor thermal conductivity means that defects on the inside of the rotor blades can often not be detected with the conventional heat flow tests. The newly developed thermography robot now makes this possible for the first time. It is inserted into the inner cavity of the rotor blade and then travels along the blade by remote control.
Investigating the heat flow
Heat thermography methods are already successfully used on the outside of rotor blades. Researchers around the Fraunhofer WKI have further developed this knowledge for the robot for use on the inside of rotor blades. The team designed the mobile thermography robot together with several industrial and research partners. As it moves down the blade from the inside, it heats the rotor blade using an infrared radiant heater. Damaged areas such as cracks, bonding defects or air pockets have a deviating thermal conductivity and therefore change the heat flow and thus the temperature distribution on the surface. The thermographic camera built into the robot records these changes and converts them into images. The robot also takes high-resolution optical photos with a camera and measures the internal geometry of the rotor blade. This makes it easier to assess material defects visible on the surface.
As the robot works both with rotor blades lying on the ground and with already installed rotor blades, this innovative method can make an important contribution to quality control, both in the production process and in the regular inspection of installed blades.