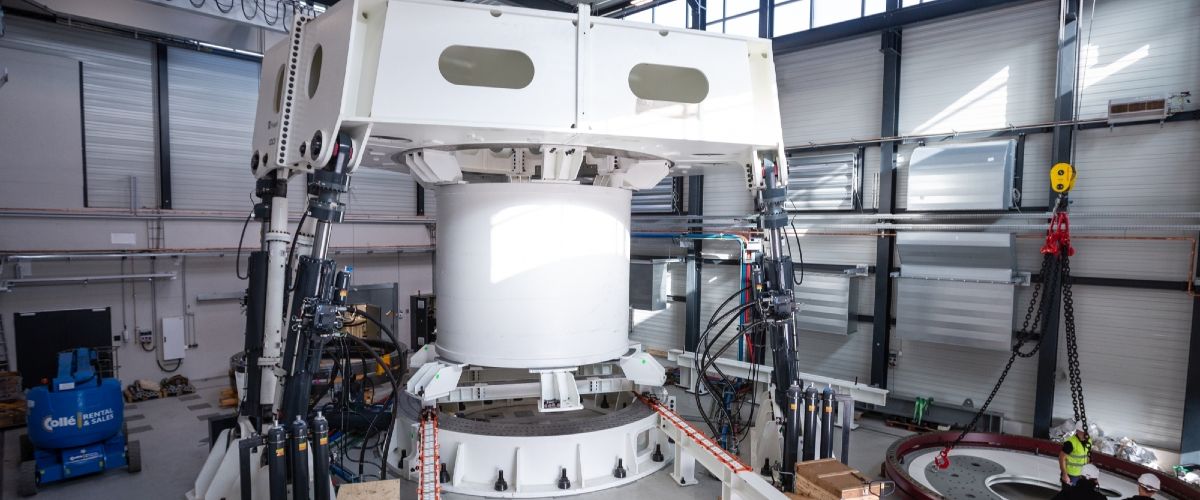
Wind energy
Test rig for rotor blades of wind turbines
The Fraunhofer Institute for Wind Energy Systems has successfully commissioned a test rig for rotor blade bearings with up to 6.5-metre diameters in Hamburg. The large-scale test rig will be used to develop new methods for designing and configuring blade bearings that can minimise yield losses.
Manufacturers and operators will benefit from the BEAT 6.1 large-diameter bearing test rig: accelerated testing can increase the reliability of large-diameter roller bearings and pave the way for new calculation methods and designs. Bearings can be validated on the test rig long before they are used for the first time on wind turbines, which was previously not possible in this way. The aim is to reduce the development costs and yield losses in order to make the operation of wind turbines up to 10 MW more economical.
In laboratory tests, seven hydraulic cylinders simulate the movement of rotor blades and the rotor rotation of wind turbines during operation – with all their constant load changes, which represent an immense load for roller bearings. The test facility can simulate an operating life of 20 years within six months.
The first rotor blade bearings to be tested on the test rig comprise eight bearings with a nominal diameter of five metres and a weight of 9,500 kg. They are being tested until summer 2021 in functional and endurance tests in the HAPT (Highly Accelerated Pitch Bearing Test) research project funded by the German Federal Ministry for Economic Affairs and Energy. Methods for the accelerated testing of blade bearings shall be developed together with the Institute for Machine Design and Tribology (IMKT) at Leibniz Universität Hannover and the IMO group of companies.