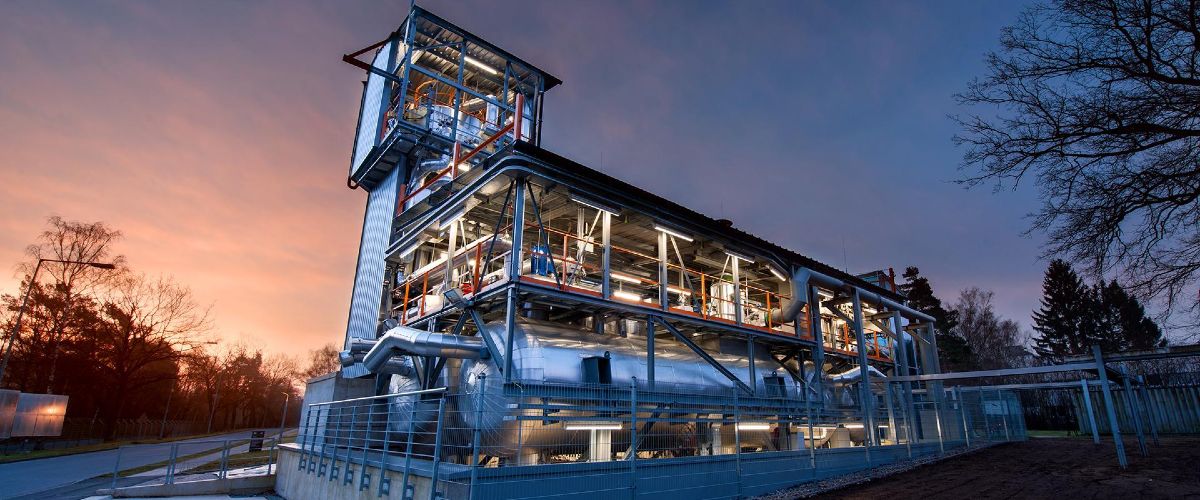
Solar thermal power plants
Liquid salt storage with heat-storing bricks
Christian Odenthal Mission Electricity Transition 2045
INTERVIEW WITH DR CHRISTIAN ODENTHAL
Bringing down the costs of liquid salt storage – that is the overarching goal of the European research project Newcline. Specifically, the team of scientists from three countries is working on a new type of single-tank concept. This involves storing the hot and cold liquid salt together in a tank. There is also heat-storing filler material in the tank. Project manager Christian Odenthal explains what this solution has in common with a latte macchiato and which work packages are pending in Newcline.
Mr Odenthal, what are the advantages of the single-tank concept with heat-storing bricks?
First of all, you simply save the cost of the second tank and also the space for it. But there are other advantages: for example, the cost of the liquid salt. This can account for up to 50 per cent of the total investment costs of a storage system. If you replace the salt for storage with an inexpensive filler - we'll use moulded bricks here - it only costs a fraction, as you need much less salt for storage. The more fillers you can pack into the tank, the cheaper it becomes. Another advantage: The tanks always require a salt sump about 60 centimetres high at the bottom. This reduces the actively used tank charge. With two tanks, you have twice the volume of unused tank space.
And how can storage be implemented in just one tank? Most solar thermal power plants use two, after all.
That's true. Until now, the salt has usually been pumped from the cooler tank to the solar receiver, where it is heated to over 500 degrees and stored in the "hot" tank. A second circuit extracts the hot salt there for on-demand electricity production in the steam turbine. But everything can also be done in a single tank. In principle, the differently tempered liquid salt behaves like the milk and the hot espresso in a latte macchiato glass. With a latte macchiato, you have the warm milk at the bottom and the hot coffee on top. Because the hot coffee has a lower density, it stays on top and does not mix with the colder milk. In the same way, the hot salt at the top has a lower density than the cold salt at the bottom. The difference in density is about 10 per cent.
What specific filler materials are being researched in the Newcline project?
We are currently working with our German partner Kraftblock on moulded bricks made of sensitive storage material. In a later work package, we also want to experiment with latent thermal storage materials. One of our European partners, the Universitat Politècnica de Catalunya from Barcelona, is coming on board for this. Latent thermal storage materials can stabilise the outlet temperature of the salt in the storage tank. We are considering encapsulating them and positioning them above the moulded bricks.
What have you already achieved so far?
The material development for the fillers has been completed and a suitable geometric shape has also been identified. We have opted for a honeycomb geometry. In this shape, the fillers can be optimally inserted into the round baskets in the round tank.
What research is currently underway?
In Barcelona, the fillers will soon be trialled in a furnace. The central question is whether the fillers remains sufficiently stable at high temperatures. This is a prerequisite for ensuring that no significant material components from the filler dissolve in the salt. In addition, we are currently using simulation software at the German Aerospace Center to calculate how the storage tank should be designed on a large scale. The digital tool can be used to calculate many different configurations in parallel and thus find a so-called Pareto optimum.
What is a Pareto optimum in storage tank?
This is a condition where the various parameters of the storage tanks design are in the best possible balance. There is no one optimal design for this. Similar to motors: These have great output but high fuel consumption and vice versa. With our fillers, it would be best if they had many tiny little ducts so that they have as large a surface area as possible with which to transfer the heat. However, this is not technically feasible. After all, the fillers have to be mechanically strong enough. Here again, it’s important to consider the large surface area where the salt can react on the brick. The simulation tool finds the parameters that are thermodynamically optimal.
What steps still need to be taken at DLR before the tests start in the TESIS test facility in Cologne?
We still have to make adjustments to the three baskets that are to be placed on top of each other in the six-metre-high tank. Previous research projects have shown that so-called bypass flow occurred at the edges of the baskets. The salt is supposed to flow through the baskets. But up to now, about 25 per cent of the flow made its way between the edge of the tank and the baskets. The background to this is that there is free space here in the previous design, partly due to the attachment of the baskets and lifting lugs. We need to address this. The baskets must no longer have any rim current.
Is the storage concept pursued in Newcline only interesting for solar thermal power plants?
No, other applications are conceivable for this. In the area of conventional fossil fuel-fired power plants, for example, high-temperature storage offers the potential to make them more flexible or to convert them into thermal storage power plants. Another area of application is energy-intensive industrial processes. At the DLR, we are currently conducting very specific research in another research project funded by the Federal Ministry for Economic Affairs and Climate Protection called TransTES-Chem to integrate a liquid salt storage facility in a chemical park.
The interview was conducted by Ilse Trautwein, science journalist at Project Management Jülich.