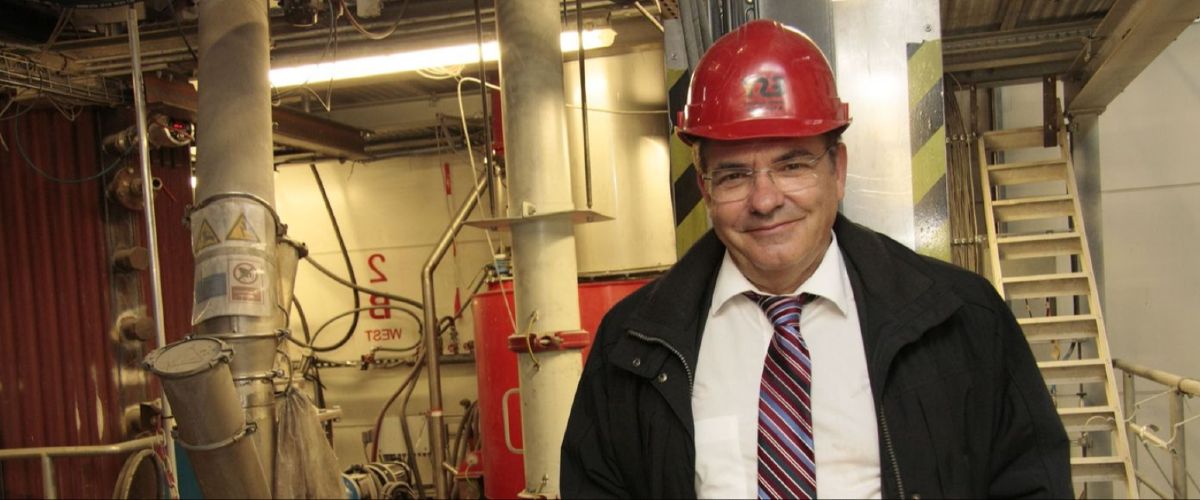
Thermal power plants
Incinerated waste as electricity storage
Bernd Epple Mission Electricity Transition 2045
INTERVIEW WITH PROF. DR BERND EPPLE
When waste is incinerated, the CO2 it contains is released into the atmosphere. Harnessing this CO2 instead to support the energy transition in the electricity sector is a new approach. The TU Darmstadt has tested a new method as part of the MONIKA project. The starting point is a problem that operators of waste incinerators are facing increasingly: remuneration. They can no longer get rid of their electricity at any time, explains project coordinator Professor Bernd Epple.
Professor Epple, what is the current situation for waste incinerators?
We can already see that there are times of electricity oversupply due to the volatile electricity injection from renewable energy sources. Then it costs money to feed the electricity into the grid. This situation will be exacerbated by a higher share of renewable energy sources. However, waste incinerators cannot simply be shut down; they have to burn the waste.
So what is your approach?
The idea is to replace the production of power with that of alternative products for which there is always a market. In this case that would be methanol, a chemical product, an alcohol. It can be used in both the industrial and the transport sector. It can be added to petrol or refined into a diesel substitute, which results in much lower emissions. This is a classic case of sector coupling. The method can also be seen as an electricity storage facility. We store power in the form of methanol and can even draw surplus electricity from the grid. We investigated this concept with significant support from our project partner SUEZ within the MONIKA project.
You are now using power and the CO2 from the plant's exhaust gases to produce methanol. Can you briefly explain the method?
The initial focus is to remove CO2 from the exhaust gas. Here it is convenient that CO2 reacts readily with calcium oxide, which results in calcium carbonate. We therefore convert this gaseous substance CO2 into a solid substance that can be separated from the exhaust tract relatively easily. In a second reactor, the calciner, we release the CO2 again by raising the temperature from 650 to 900 degrees Celsius. The novelty at MONIKA is that we now use waste instead of coal. Mainly non-recyclable plastic waste, which also contains wood with a biogenic content. This means that we even have a CO2 sink in the overall balance; we withdraw the CO2 stored in the wood from the cycle.
What happens to the CO2 then?
For this we have the surplus electricity that we do not want to feed into the grid. We use it for the electrolysis of water into hydrogen and oxygen. We need the hydrogen for the synthesis of methanol. We use the oxygen to release the CO2 in the calciner. You tested the method in your pilot plant, which you have been operating since 2009 with regard to CO2 separation with calcium oxide.
What are your findings?
The plant runs very stable with various coals and now also very well with the tested alternative fuel from waste, which we have used here for the first time worldwide for this method. This enables us to achieve over 90 per cent CO2 separation from the tested exhaust gases.
The end result is a concept for the possible retrofitting of existing waste incinerators. For which plants can it be used?
Ultimately this can be retrofitted to all types of incinerators. From a technical point of view there is no problem at all. Pure CO2 separation with this method is also already outstanding from an economic point of view. Compared to all other CO2 separation processes, we are more than 50 per cent cheaper. However, if we want to produce methanol, electrolysis is a cost factor that must become even cheaper. This is currently being further developed in Germany and worldwide.
Your aim is to test the new method in a demonstration installation. What is the current status here?
We are currently in the process of designing a demonstration installation with a thermal capacity of 10 megawatts. This will increase the output by a factor of 10 compared to our existing pilot plant. The fuels used are waste, especially plastic waste. We are planning to construct the plant as part of a real-world laboratory. The German Federal Ministry for Economic Affairs and Energy (BMWi) is funding "real-world laboratories of the energy transition", where innovations can be investigated on an industrial scale and in real environments. In addition to technical aspects, operators of large waste incinerators are particularly interested in the costs incurred when the new CO2 capture technology is retrofitted. We have carried out a cost estimate and would like to prove this with the help of the new plant.
What other exciting projects are you working on?
We are currently working on further innovative energy conversion processes. For example, we are researching the chemical recycling of various non-recyclable plastic wastes. The work is based on experience gained within the BMWi project FABIENE – only that we do not use coal but plastic waste as fuel. The fuel, that is the plastic, is not burned but gasified. The synthesis gases can be used to produce chemical base materials, such as methanol. Methanol can in turn be used to synthesise high-quality new plastics.
How did you get into power plant research?
At university I studied energy process engineering with a focus on combustion processes. Afterwards I was able to gain important experience in the field of power plant planning and plant construction at my first employer ALSTOM, now General Electric Deutschland. This gave me the opportunity to lead the construction of two power plants in Shanghai as project manager. This exciting task accompanied me for several years and had a lasting impact on me.
What fascinates you personally about your work?
With our research work at the TU Darmstadt, I can contribute to offering technical solutions, for example to separate climate-harming CO2 from exhaust gases using the carbonate looping process and to prepare it for further processes. Ultimately, we synthesise chemical base materials from the separated CO2, which can be further processed. It is also fascinating to get young, motivated employees excited about such work. I can pass on my experience and watch people grow with their tasks.
The interview was conducted by Meike Bierther, science journalist at Project Management Jülich and Micaela Münter, science journalist at FIZ Karlsruhe.