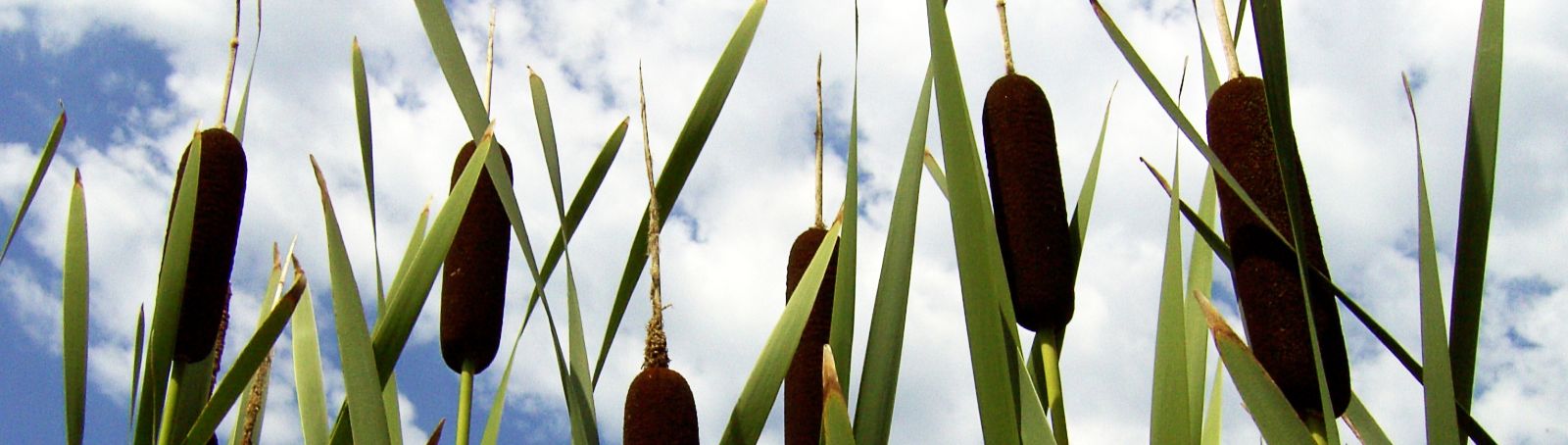
Klimafreundlich vom Feld bis zur Baustelle
Mit Rohrkolben nachhaltig und effektiv dämmen
Gebäude müssen energieeffizienter werden. Doch viele bewährte Dämmstoffe sind zwar wirkungsvoll, aber nicht nachhaltig. Wie eine kreislaufgerechte Alternative aussehen kann, hat das Forschungsprojekt RokoDaMi gezeigt. Die hier entwickelten Platten sollen erdölbasierten Dämmstoffen Konkurrenz machen.
Der Rohrkolben (lateinisch Typha) ist ein wahrer Alleskönner. Auf der gleichen Fläche bindet die Moorpflanze deutlich mehr CO2 und liefert einen bis zu fünfmal höheren Ertrag als ein hiesiger Nadelwald. Wegen seiner besonderen Eigenschaften eignet sich der Rohrkolben außerdem ideal für die Herstellung von Dämmstoffen: Seine Blätter bestehen aus einem faserverstärkten Stützgewebe gefüllt mit einem weichen Schwammgewebe. Diese Kombination macht die Pflanze gleichzeitig stabil und leicht, was in Typha-Dämmstoffen für eine hohe Festigkeit und eine gute Dämmwirkung sorgt. Typha-Produkte sind wegen ihres hohen Anteils an Polyphenolen außerdem von Natur aus feuchtigkeits- und schimmelresistent. Dadurch kann bei der Verarbeitung auf Chemikalien verzichtet werden, was das Endprodukt zu 100 Prozent ökologisch und kompostierbar macht.
Nachwachsende Rohstoffe sind auf dem deutschen Dämmstoffmarkt jedoch immer noch vergleichsweise selten vertreten. Am beliebtesten sind in diesem Segment Holzfaserprodukte, die in der Herstellung aber je nach Verfahren sehr energieintensiv sind. Bei der Produktion von einem Kubikmeter Holzfaserdämmstoff im Nassverfahren wird so viel Energie benötigt, dass damit ein durchschnittlicher Haushalt mit zwei Personen mehr als drei Monate lang mit Strom versorgt werden könnte.
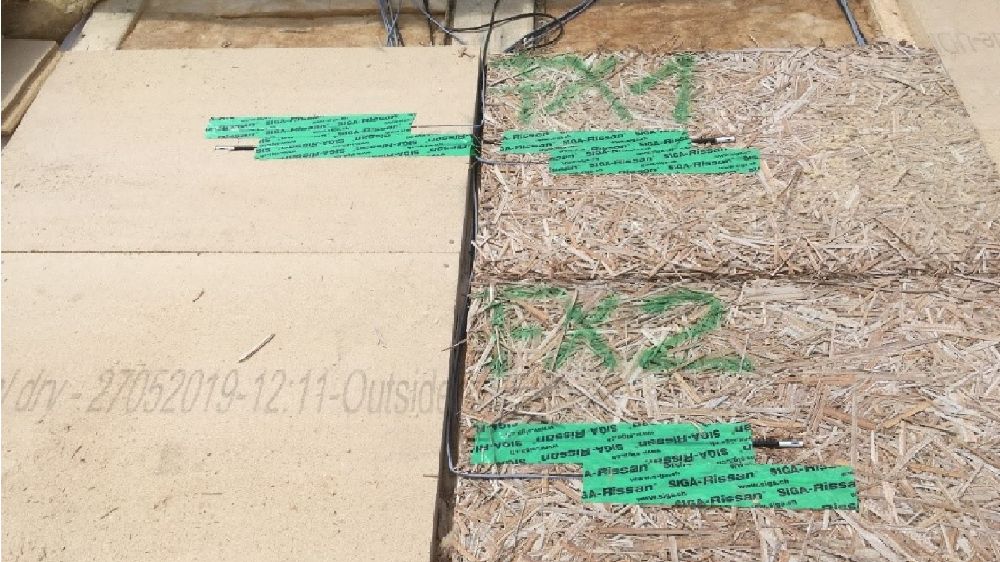
Typha-Dämmstoff in Kombination mit einem mineralischen Bindemittel kann hingegen einfach an der Luft trocknen. Trotz dieser guten Voraussetzungen ist Typha am Markt bisher ausschließlich als Nischenprodukt zu finden und wird beispielsweise bei der Sanierung von Fachwerkhäusern eingesetzt.
Das wollte das Team des Forschungsprojekts RokoDaMi ändern und hat eine Aufdachdämmung aus Rohrkolben entwickelt, die auch bei Preis und Leistung mit herkömmlichen Materialien konkurrieren kann. Das Fraunhofer Institut für Bauphysik (IBP), der Dämmstoffhersteller Saint Gobain Isover und der Materialspezialist Typha Technik Naturbaustoffe variierten dazu Material und Zusammensetzung, testeten bereits etablierte Produktionsanlagen für die Anwendung mit Typha und demonstrierten den Einsatz der so entstandenen Typhaboards an zwei Testflächen. Die Projektpartner erarbeiteten außerdem ein Konzept zur industriellen Umsetzung, das im Abschlussbericht von RokoDaMi beschrieben wird.
Bessere Dämmleistung durch optimierte Schnitttechnik
Wesentliche Ziele des Vorhabens waren die Reduzierung der Wärmeleitfähigkeit auf unter 0,045 Watt pro Meter mal Kelvin (W/mK) und die Reduzierung der Rohdichte auf unter 200 Kilogramm pro Kubikmeter (kg/m³), ohne dabei Abstriche bei der Festigkeit im Vergleich zu Konkurrenzprodukten machen zu müssen. Ähnliche Werte sind auch bei Holzfaserdämmstoffen üblich.
Bereits bei der Schnitttechnik gab es Optimierungsbedarf: Die Forschenden stellten fest, dass Rohdichte und Wärmeleitfähigkeit am besten mit größeren Typha-Partikeln verringert werden können, da diese eine geringere Oberfläche haben und deshalb weniger Bindemittel benötigen. Doch die Platten waren mit den größeren Partikeln nicht mehr abriebfest genug für eine Aufdachdämmung. Die Lösung: Ein mehrschichtiges System mit großen Partikeln im Inneren und kleinen Partikeln als Deckschicht. Um beide Größen herstellen zu können, wurde die Schneideanlage entsprechend angepasst. Der Prozess wurde außerdem so optimiert, dass nur die Teile der Pflanze mit den besten Dämmeigenschaften weiterverarbeitet wurden.
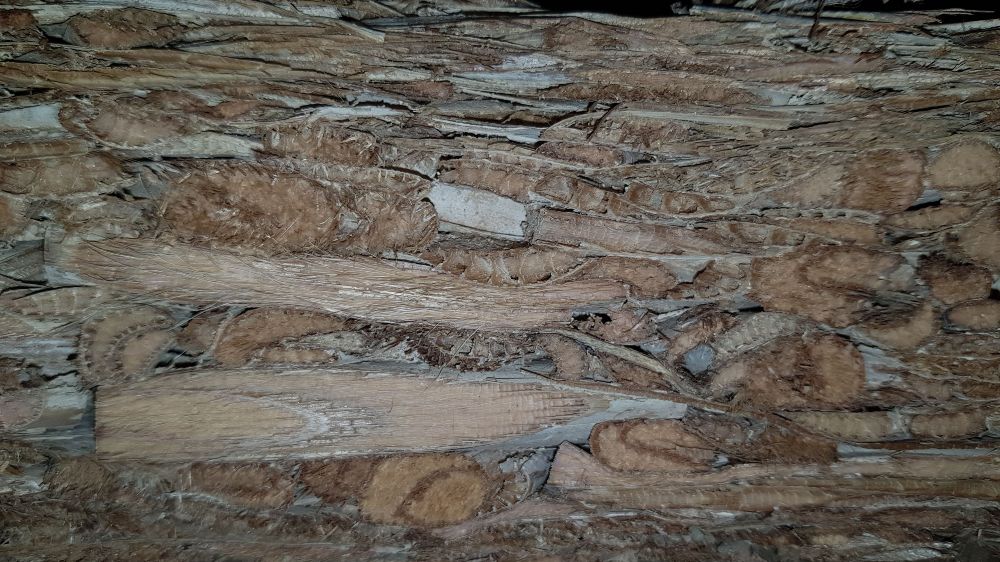
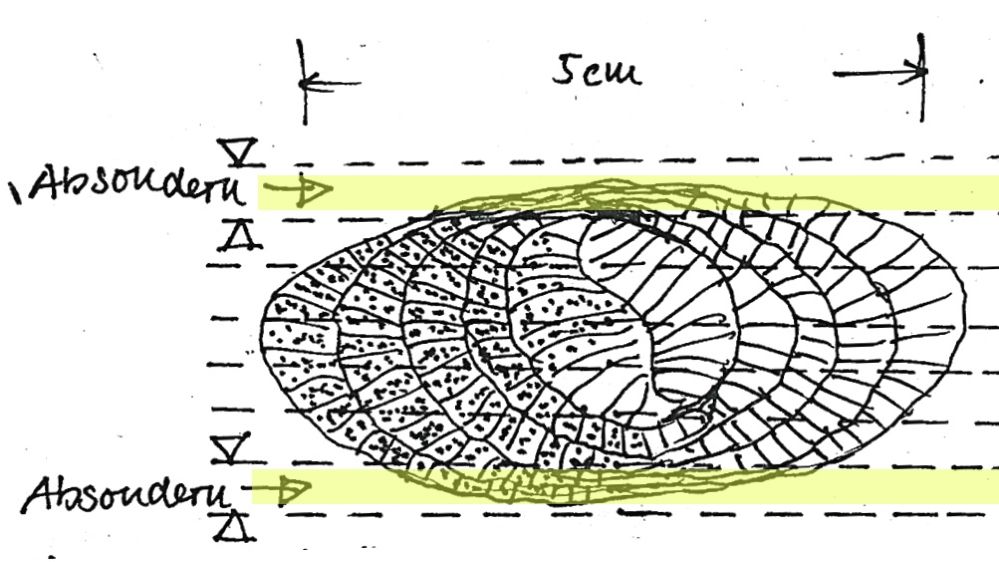
Zu 100 Prozent ökologisch mit mineralischem Bindemittel
Neben den Typha-Blättern ist das Bindemittel der zweite wichtige Bestandteil des Dämmstoffs. Die Forschenden stellten mehrere Probeplatten mit verschiedenen Stoffen her und testeten diese auf Rohdichte, Festigkeit und Wärmeleitfähigkeit. Die besten Ergebnisse erzielte Magnesit: Im Vergleich mit Kasein hatten die Magnesit-Platten etwa 60 Prozent höhere Zug- und Druckfestigkeiten und eine mehr als doppelt so hohe Biegefestigkeit. Zement jedoch, der standardmäßig bei der Herstellung von Holzfaserdämmplatten zum Einsatz kommt, stellte sich als ungeeignet heraus.
Magnesit überzeugte außerdem bei Tests zum Brandschutz. Die Platten neigten im Gegensatz zu Holzfaserprodukten nicht zum Glimmen und konnten in die Euroclass B eingeordnet werden – die beste Einstufung, die ein Material mit brennbaren Bestandteilen erreichen kann. Hinzu kommt der ökologische Vorteil: Durch das organische Bindemittel ist die Typha-Magnesit-Dämmplatte vollständig kompostierbar. In der Anwendung werden die Platten außerdem lediglich miteinander verschraubt, sodass auch ein Rückbau problemlos möglich ist. Sie können dann entweder in einem anderen Gebäude wiederverwendet oder geschreddert und kompostiert werden.
Mit dem dreischichtigen Aufbau, gröberen Typha-Partikeln und damit auch geringerem Bindemittelbedarf erreichte das RokoDaMi-Team sein gestecktes Ziel: Die Rohdichte der Platten konnte von 270 kg/m³ um mehr als 40 Prozent auf etwa 155 kg/m³ gesenkt werden. Dadurch ergab sich auch ein um etwa 35 Prozent niedrigerer Diffusionswiderstand, was gerade beim Einsatz als Aufdachdämmung von Vorteil ist. Durch die verringerte Rohdichte in Kombination mit der verbesserten Partikelqualität konnte die Wärmeleitfähigkeit außerdem deutlich unter 0,045 W/m2K abgesenkt werden. Die nötige Festigkeit für eine Aufdachdämmung blieb dabei trotzdem erhalten. „Das Typhaboard ist ein Produkt aus einem nachwachsenden Rohstoff, das nicht nur viele Vorteile für Umwelt und Klima mit sich bringt, sondern auch mit seinen technischen Eigenschaften überzeugt“, fasst Projektleiter Prof. Dr. Martin Krus vom Fraunhofer IBP die Ergebnisse zusammen.
Neues Produkt, etablierte Produktionsanlagen
Um das Produkt auf Dauer konkurrenzfähig produzieren zu können, bot es sich an, bestehende Fertigungsanlagen für die Verarbeitung von Typha zu testen. Die Projektpartner nutzten dazu erfolgreich die Anlage eines Herstellers von Holzwolle-Leichtbauplatten (HWL) und konnten dort mit kleineren Anpassungen Typha-Platten herstellen. Noch bessere Ergebnisse erzielte jedoch eine Technologie zur Fertigung von Spanplatten an einer Versuchsanlage der Universität Göttingen. Hier kamen die oben beschriebene optimierte Schnitttechnik und die verbesserte Plattenstruktur mit großen und kleinen Partikeln zum Einsatz. Nachdem klar war, dass sich die Anlage generell für Typha-Produkte eignet, wurden mehrere Platten unter industrie-ähnlichen Bedingungen für einen Praxistest hergestellt. So konnten die Forschenden realitätsnahe Erfahrungen für die Konzeptionierung eines industriellen Prozesses machen und die Fertigung weiter optimieren. Ein wesentliches Ergebnis war dabei eine Methode zur schnelleren Aushärtung der Platten. Nach der Durchströmung mit Heißdampf konnten diese bereits nach zwei bis drei Minuten ausgeschaltet werden. „Der Prozess wird so beschleunigt und damit deutlich kostengünstiger“, erklärt Krus. „Für eine erfolgreiche Bandproduktion ist das eine wichtige Grundvoraussetzung.“ Dabei bleibt die Typhaboard-Herstellung im Vergleich zu Holzfaserprodukten trotzdem energiearm. Denn trocknen können die Platten nach dem Ausschalen einfach an der Luft.
Typha-Dämmung überzeugt im Praxistest
Auch in der Anwendung konnten die guten Ergebnisse der Vorversuche bestätigt werden. Das RokoDaMi-Team installierte mehrere Dämmplatten und entsprechende Sensortechnik auf einem flexiblen Dachprüfstand des Fraunhofer IBP, das eine typische Altbausituation simuliert. Das Ergebnis: Die Typha-Aufdachdämmung eignete sich genauso gut für die nachgestellte Sanierung wie eine vergleichbare Holzfaserdämmung. Der Wärmewiderstand der beiden Varianten war durchweg ähnlich.
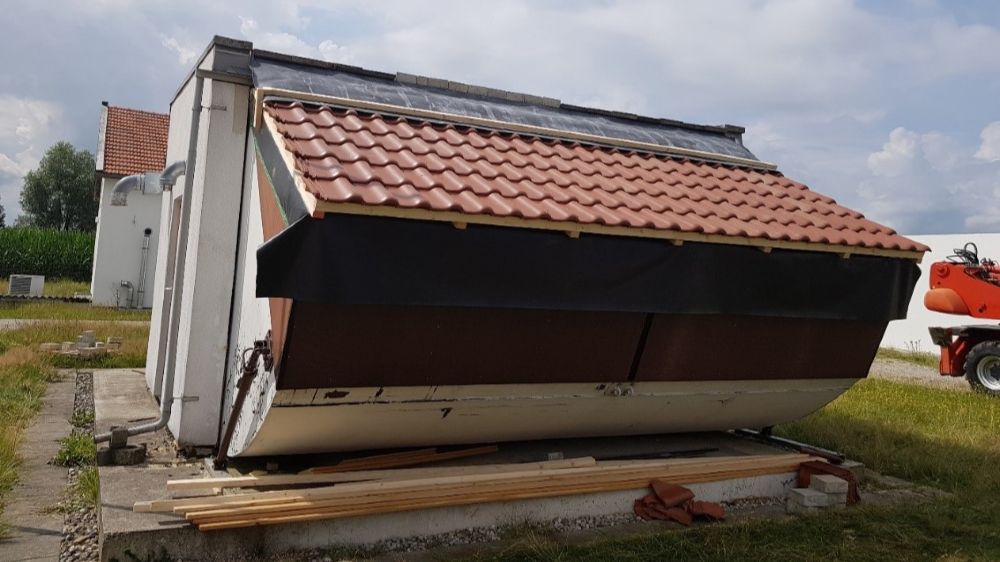
Zusätzlich wurde die Aufdachdämmung in einem Neubau angebracht. Auch dort zeigte die ermittelte Wärmeleitfähigkeit eine gute Übereinstimmung mit den Laborergebnissen und war tendenziell sogar noch niedriger.
Konzept für die industrielle Herstellung
Die Forschenden schätzen, dass eine kleine Fertigungsanlage für Typha-Platten mit einer Investition von rund 890.000 Euro aufgebaut werden könnte. Bei einer täglichen Produktion von acht Kubikmetern Baustoff, zu einem Preis von 350 Euro pro Kubikmeter ab Werk, rechnen sie mit jährlichen Einnahmen von rund 560.000 Euro, bei Kosten von rund 435.000 Euro.
Größere Anlagen könnten noch effizienter produzieren, sind aber wegen der erforderlichen Rohstoffmengen aktuell nicht realistisch. Die kleinere Anlage könnte bereits mit rund 15 Hektar Anbaufläche versorgt werden.
Der heimische Anbau ist entscheidend, um Typha für den deutschen Baustoffmarkt effektiv nutzbar zu machen, erklärt Diplomingenieur Werner Theuerkorn vom Projektpartner Typha Technik: „Es gibt zwar große Rohrkolbenbestände in Osteuropa, für eine deutsche Produktion sind diese aber zu weit entfernt“, sagt er. „Typha hat anders als Holz ein sehr geringes spezifisches Gewicht. Der Transport großer Mengen über lange Strecken wäre daher kostenintensiv und nicht nachhaltig.“ Der Anbau vor Ort hätte außerdem noch andere positive Effekte, wie die Möglichkeit, wiederverwässerte Moore landwirtschaftlich zu nutzen.
Insgesamt hat RokoDaMi gezeigt, dass eine Typha-Aufdachdämmung mit herkömmlichen Anlagen konkurrenzfähig hergestellt werden kann. Die so gewonnenen Erkenntnisse sind außerdem auf andere Typha-Produkte übertragbar. „Mit Blick auf die angeschlagenen heimischen Wälder ist zukünftig auch Holzersatz ein Thema“, sagt Theuerkorn. „Im Bauholzbereich könnten Typha-Produkte mit geringem Gewicht, hoher Festigkeit und guten Dämm- und Brandschutzeigenschaften punkten.“ Möglich sei beispielsweise eine USB-Platte aus Rohrkolben. Die in RokoDaMi entwickelte Aufdachdämmung wurde außerdem auch nach Ende der Projektlaufzeit weiter optimiert. (ks)