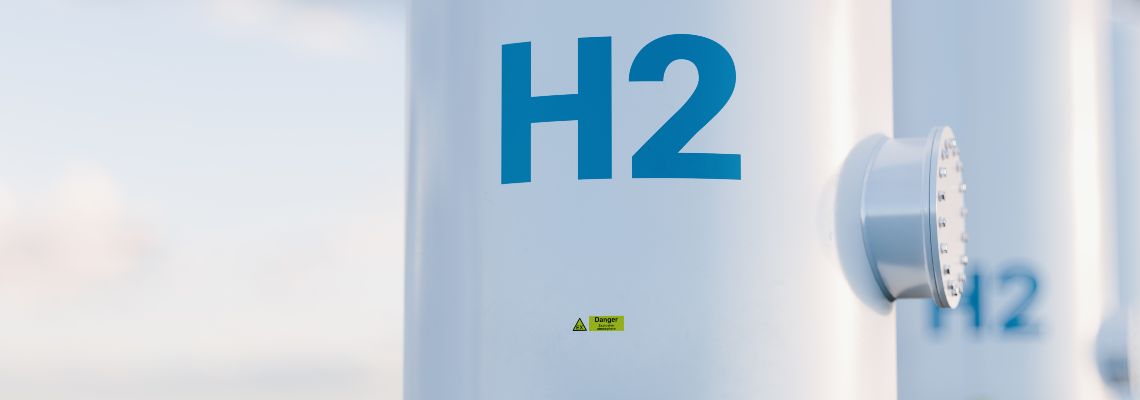
Elektroden unter Beschuss
Wasserelektrolyse effizienter machen
Dem Forschungsteam im Verbundprojekt GREENH2 ist es gelungen, die Elektrodenmaterialien von Elektrolyseuren zu verbessern und gleichzeitig einen effizienten und günstigen Herstellungsprozess für die Massenproduktion entwickeln.
Ein vielversprechendes Anwendungsfeld von Power-to-Gas-Anlagen ist der flexible Einsatz, der sich am aktuellen Angebot an erneuerbarer elektrischer Energie im Stromnetz orientiert. Wird zu viel Strom produziert, wird er in den Anlagen genutzt, um Wasser in Wasserstoff und Sauerstoff zu zerlegen.
Diese Technologie kann dadurch nicht nur das Stromnetz entlasten, sondern ermöglicht auch eine zeitliche entkoppelte Nutzung der regenerativ erzeugten Energie in Form von Wasserstoff. Die heute existierenden alkalischen Elektrolyseure sind allerdings aufgrund ihres Elektrodenmaterials für den fluktuierenden Betrieb nicht gut geeignet.
Elektrolyseur spaltet Wasser in Wasserstoff und Sauerstoff
Um Wasser in Wasserstoff und Sauerstoff zu spalten, wird an eine Elektrolysezelle eine elektrische Spannung angelegt, die sich aus einer definierten Mindestspannung – der sogenannten Zersetzungsspannung – und aus zwei Überspannungen zusammensetzt. Damit kann an den beiden Elektroden jeweils eine Teilreaktion bei hohen Stromdichten ablaufen. Wie viel Überspannung für eine Reaktion nötig ist, hängt vom Material der Elektroden ab.
„Je größer die Oberfläche des Materials, desto geringer ist die benötigte Überspannung, heißt, desto effizienter ist die Elektrolyse“, erklärt Wolfgang Schade, Professor am Fraunhofer Heinrich-Hertz-Institut HHI und Verbundkoordinator des Projekts GREENH2. „In heute üblichen Elektrolyseuren besteht die Elektrode meist aus porösen Raney-Nickel-Strukturen. Diese haben zwar eine große Oberfläche, verlieren aber bei starken Lastschwankungen an Wirkungsgrad.“
Laserpulse vergrößern die Oberfläche der Elektroden
Die neuen Elektrodenmaterialien hingegen sollen robust gegenüber Lastschwankungen sein und müssen mit einer größeren Oberfläche versehen werden. Dazu hat Verbundpartner Fraunhofer IFAM ein Fertigungsverfahren auf Basis von Lasertechnologie entwickelt.
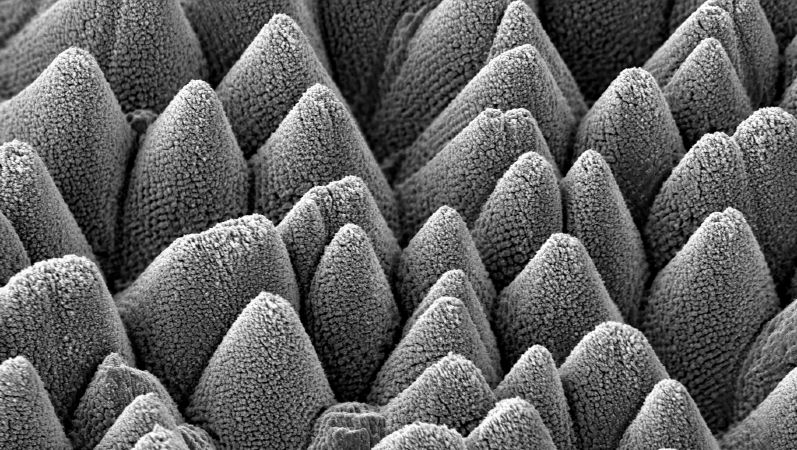
Ein Hochleistungslaser – eine Ultrakurzpulslaserstrahlquelle von Verbundpartner AMPHOS – schießt mit einer Ausgangsleistung von mehreren hundert Watt und Pulsdauern von weniger als einer Picosekunde (eine billionstel-Sekunde) auf ausgewählte Metalloberflächen.
„Mit diesem Verfahren sind wir in der Lage, möglichst einfach und effizient die Oberfläche der Elektroden so zu strukturieren, dass entsprechend niedrige Überspannungen möglich sind“, erklärt Dr. Lars Röntzsch, Abteilungsleiter Wasserstofftechnologie am Fraunhofer IFAM.
„Im Vergleich zu anderen Verfahren, die Oberflächen funktionalisieren, ist unsere Methode wesentlich eleganter und in größerem Maßstab auch günstiger.“
Elektroden werden im Einsatz getestet
Im Vorfeld habe das Team von Lars Röntzsch diesen Vorgang im Labormaßstab von wenigen Quadratzentimetern getestet.
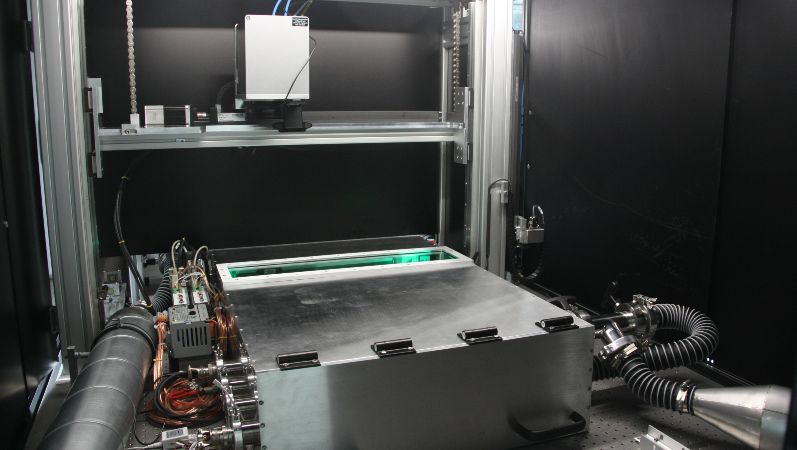
„Im Rahmen des Projekts haben wir eine Demonstrator-Fertigungsanlage auf dem EnergieCampus Goslar aufgebaut, wo wir nun auch Oberflächen von einem halben Quadratmeter Größe funktionalisieren können“, erklärt Dr. Lars Röntzsch.
In einem Versuchselektrolyseur am Fraunhofer IFAM sollen die verschiedenen Elektrodenmodelle dann im Einsatz getestet werden.
„Wenn alles funktioniert, können die optimierten Elektroden in großer Stückzahl produziert und verbaut werden und damit auch den Markt für Power-to-Gas-Anlagen in Deutschland vorantreiben. Denn der wird im Zuge der Energiewende stark wachsen. Deutschland hat hier das Potenzial, sich zum Leitmarkt zu entwickeln – wenn wir rechtzeitig in die Optimierung dieser Anlagen investieren“, erklärt Wolfgang Schade.