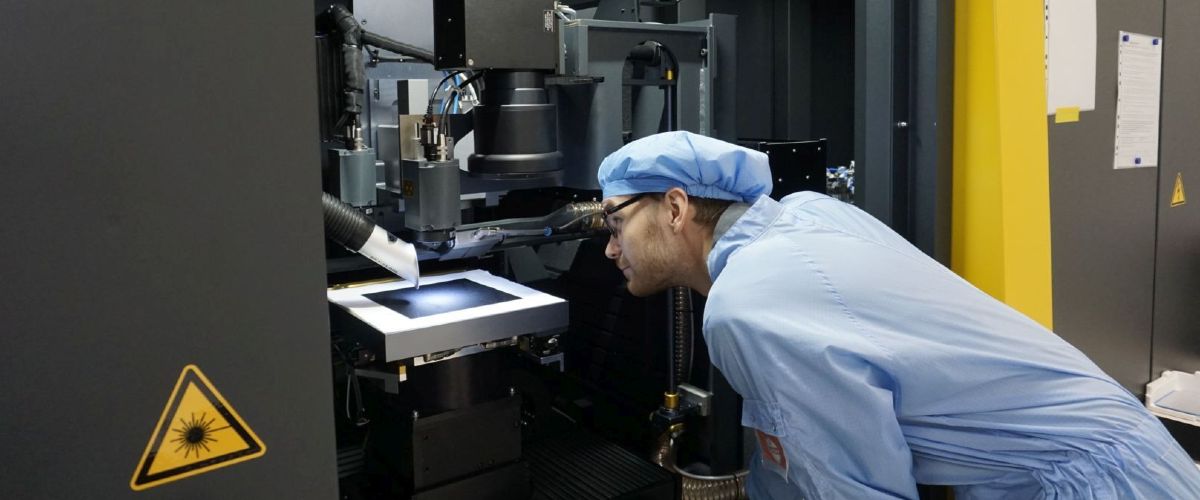
Photovoltaik
Solarzellenkontakte per Laser hergestellt
Das neu entwickelte Verfahren ist besonders für temperaturempfindliche Zellkonzepte geeignet.
Forscherinnen und Forscher haben in dem Verbundvorhaben C³PO ein Laser-Kontaktierungsverfahren weiterentwickelt, mit dem Solarzellenkontakte hergestellt werden. Innerhalb des Projekts wurde das am Fraunhofer Institut für Solare Energiesysteme (ISE) entstandene „Laser Transfer and Firing“ Verfahren, kurz LTF, optimiert und erstmalig vollautomatisiert auf einer industrienahen Anlage umgesetzt. Bei dieser Technologie handelt es sich um einen Kontaktierungsprozess für schmale Kontakte aus Kupfer mit einer Breite von 20 Mikrometern.
Der konkrete Ansatz des LTF-Verfahrens bietet eine Alternative, um Solarzellenkontakte herzustellen. Auf jeder Solarzelle sind metallische Leiterbahnen aufgebracht. Diese werden als Kontaktfinger bezeichnet und sind notwendig, um den in der Solarzelle erzeugten Strom abzuleiten. Der industrielle Siebdruck ist das üblicherweise genutzte Verfahren, mit dem die Kontaktfinger aufgebracht werden. Neben dem Siebdruck, bei dem Silberpaste auf der Vorderseite der Solarzellen aufgebracht wird, gibt es jedoch weitere Verfahren zur Kontaktierung. Hierbei werden anstelle von Silber beispielsweise alternative und günstigere Metalle verwendet. Zum einen kann dadurch Edelmetall eingespart werden, zum anderen ergeben sich Vorteile bei bestimmten Solarzellenoberflächen. An dieser Stelle setzt LTF an.
Beschichtungs- und Laserprozess im LTF-Verfahren
Das LTF-Verfahren setzt sich aus zwei Schritten zusammen. Zunächst muss das jeweils für die Solarzelle spezifische Layout der Kontaktfinger auf selbige übertragen werden. Dazu wird mittels eines Laserdruckverfahrens Metall von einer beschichteten Folie auf die Solarzelle aufgebracht. Je schmaler das metallische Kontaktfingerlayout ist, desto weniger werden eintreffende Sonnenstrahlen abgeschattet. Der gesamte Arbeitsschritt wird als „Laser Induced Forward Transfer“ (LIFT) bezeichnet.
Für den LIFT-Prozessschritt in der neuen LTF-Anlage wird die Solarzelle zunächst auf einem Vakuum-Chuck positioniert und anschließend unter eine metallbeschichtete Trägerfolie gefahren. Von dieser wird das Metall auf die Solarzelle übertragen. Im nächsten Schritt kann die Metallfolie vollautomatisch durch ein Rolle-zu-Rolle-System ein Stück weiter transportiert werden. Schließlich wird eine neue Zelloberfläche herangefahren und das nächste Metallgitter auf sie übertragen. In Kooperation zwischen ROWO Coating und ISE wurden für diesen Prozessschritt speziell beschichtete Folien entwickelt, um die besonderen Anforderungen an das oben beschriebene Schichtsystem zu erfüllen. Die Aufskalierung der so entwickelten Schichtsysteme auf Industriebeschichtungsanlagen wurde bei ROWO Coating durchgeführt. Das Unternehmen ist auf die Beschichtung von flexiblen Substraten von Rolle-zu-Rolle spezialisiert, wobei verschiedene Vakuumbeschichtungsverfahren eingesetzt werden.
Nachdem die Trägersubstrate beschichtet wurden, müssen im zweiten Schritt des LTF-Prozesses noch die Kontaktfinger hergestellt werden. Dies erfolgt über „Laser Selective Heating“ (LSH). Im LSH-Prozessschritt werden die auf der Oberfläche der Solarzelle entstandenen Metallstrukturen mit einem Laser zu Kontakten bearbeitet.
Neben dem Fraunhofer ISE und ROWO Coating waren an den Projektarbeiten weiterhin die Unternehmen Pulsar Photonics, Soliton und Rena beteiligt.
Neues Kontaktierungsverfahren besonders für Heterojunction-Solarzellen geeignet
Der LTF-Prozess wurde innerhalb des Verbundprojekts jetzt erstmalig auf einer Industrieanlage vollständig automatisiert abgebildet. Er legt damit die Basis für zukünftige Weiterentwicklungen in diesem Bereich. Positiv zeichnet sich LTF bereits durch die flexibleren Wahlmöglichkeiten der verwendeten Metalle aus und die damit verbundenen gestalterischen Optionen beim Layout der Kontaktfinger. Darüber hinaus ist das Verfahren auch speziell für Solarzellen geeignet, die temperaturempfindliche Schichten enthalten. Insbesondere Heterojunction-Solarzellen, bei denen kristalline Siliziumwafer mit Dünnschichttechnologie kombiniert werden, profitieren davon. Dieses Zellkonzept ergibt hohe Wirkungsgrade, erlaubt aber keine hohen Temperaturen bei der Produktion. Der im letzten Schritt genutzte Laser bildet deshalb lediglich die Kontakte aus, ohne dabei die Solarzelle zusätzlich zu erwärmen. Dies wiederum beeinflusst den Wirkungsgrad der Solarzelle positiv.